Embodied Carbon in Buildings and Climate Change
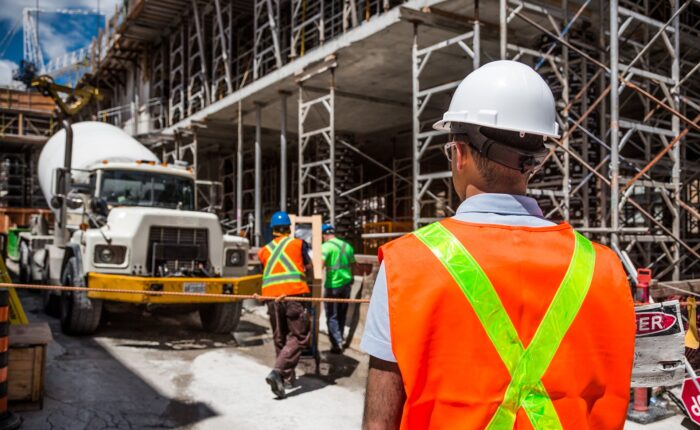
Building operations and building construction industry emissions together were responsible for 38% of global energy-related carbon dioxide emissions in 2019. About three quarters of that consisted of building operations such as heating, cooling, and lighting. The remaining but often overlooked one quarter was embodied carbon, which includes non-operational emissions and is defined by the World Green Building Council (WGBC) as “carbon emissions associated with materials and construction processes throughout the whole lifecycle of a building or infrastructure”. This includes emissions from raw material extraction, transportation of raw materials to a factory, manufacturing of building materials at the factory, transportation of building materials to the building site, building construction, demolishing, and landfilling of the remaining material. The global building stock is predicted to double between 2019 and mid-century due to population growth and so ignoring building emissions will result in us not being able to meet our Paris climate goal of limiting warming to 1.5 degrees Celsius (above pre-industrial levels). Typically reducing operational emissions has been the focus so the expectation is that embodied carbon will generate a greater proportion of building emissions over time. According to the WGBC just upfront carbon, which is embodied carbon emissions due to buildings before building use, “will be responsible for half of the entire carbon footprint of new construction between now and 2050, threatening to consume a large part of our remaining carbon budget.” We thus need to focus on achieving net-zero embodied carbon – meaning that embodied carbon emissions are minimized and any remaining emissions are offset with carbon sinks.
Measuring Embodied Carbon
If a building has to be built embodied carbon can be reduced by performing a Life Cycle Assessment (LCA) before construction. An LCA for a building determines material and energy inputs and outputs for each stage of a building’s life cycle and determines corresponding environmental impacts such as climate emissions. Known as a Whole-Building LCA, these assessments use documents called Environmental Product Declarations (EPD’s) containing lifetime impacts for each building material. Countries worldwide are thus building EPD databases for materials from local manufacturers to assist in performing LCA’s for local construction projects.
According to Green Building Canada, an LCA can raise environmental impacts that would otherwise be overlooked. An example they give is that “assessing the sustainability of two similar bamboo floors isn’t so obvious unless conducting an LCA. How far did the flooring travel before eventually getting installed? How much embodied energy went into it? What effect will its disposal have?”
The results of a Whole-Building LCA, performed in the building design stage can, according to The Atmospheric Fund (TAF) report entitled “Embodied Carbon in Construction: Policy Premier for Ontario”, help reduce embodied emissions by choosing materials that can be reused or recycled, materials that require less maintenance and repair, materials that can be locally sourced, as well as materials with highly efficient manufacturing processes.
Examples Around The World
Embodied carbon reduction policies are being put in place around the world and some policy examples are worthy of mention. In Germany, a Whole-Building LCA is required for new federal building projects and a free national LCA software tool along with an EPD database for Germany has been developed to assist with this. In Sweden, large infrastructure projects must report on embodied carbon emissions and are awarded money if they are below a target. In The Netherlands, embodied carbon reporting is required for new residential and office buildings over 100 metres square.
Our Current Approach
Progress is being made in Canada to achieve embodied carbon reductions. For instance, Vancouver has set a goal to reduce embodied carbon emissions by 40% in new buildings and other construction projects by 2030. Climate calculator tools are being deployed by governments. Here in Ontario, a government spokesperson stated that a new Building Carbon Calculator tool will be launched in the next few months which “will support the increased use of low-carbon building materials in building construction” such as wood-based constructions. A tool customized for Quebec, Gestimat, is being used to estimate climate emissions from manufacturing structural materials to compare different building scenarios.
Next Steps for Ontario
Examples of next steps for Ontario to reduce embodied carbon include building a complete EPD materials database as well Whole Building LCA tools that all developers in the province can use to provide consistency when comparing buildings. Ontario also should require mandatory embodied carbon performance targets in the building code and have reporting requirements for new constructions. The province should work with municipalities to provide monetary incentives for reducing embodied carbon – such as reducing development fees. These measures will help us not lose sight of embodied carbon emissions while working to ensure that building operational emissions are reduced as well.